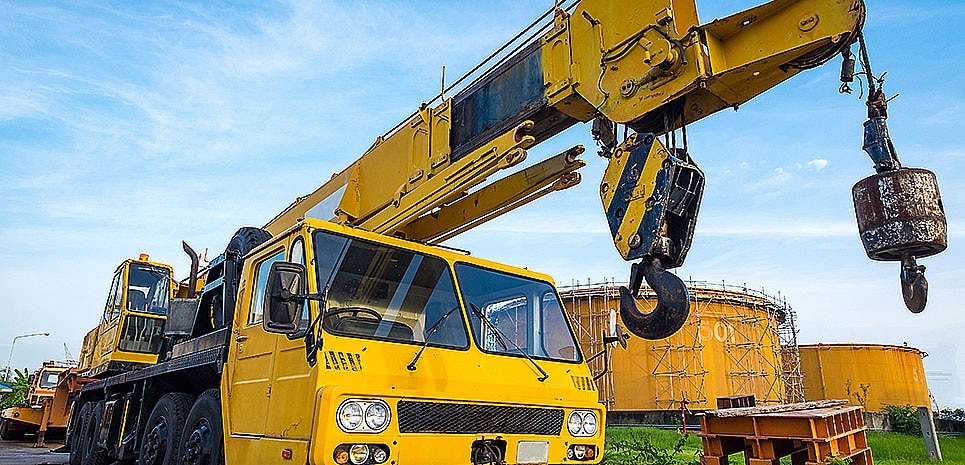
You might have come across several types of wire ropes at construction sites. These ropes are basically several strands of metal wires that are twisted to form a composite rope for crane rigging and other heavy-duty purposes. These wires help and work together to help move and support a load or an object. Let us dig a bit deeper and understand what are wire ropes used for in addition to the different types.
What Is A Wire Rope?
As mentioned previously, a wire rope is made of several strands of metal wires. These ropes are attached to a crane or hoist with a shackle or swivel to attach to a load that needs to be lifted and shifted. In addition to that, these ropes can also be used for towers and suspension bridges.
Apart from lifting and moving loads, wire ropes are used for several other reasons. Its unique design and structure provide flexibility, strength, and the ability to handle stress. Back in the day, iron was used to make metal wires, however, today steel is used. Plus, wire ropes are made from cold-drawn wires that increase durability and strength. It needs to be mentioned that as the size of the wire decreases, the strength increases.
Metal wires are made from several other materials as well such as cast steel and extra strong cast steel to improve strength. For special purposes, wire ropes can also be made from aluminum, bronze, and copper.
Types Of Wire Ropes
Wire ropes due to their unique design and structure feature flexible and tough characteristics in addition to being weather and corrosion-resistant. As a result, wire ropes are mostly used in agriculture, engineering, aircraft, and marine industries. There are three popular types of wire ropes: stainless steel wire rope, galvanized wire rope and coated wire rope.
The stainless-steel wire rope is the standard nowadays. It utilizes standard alloy in the cable and rope. As compared to the galvanized and coated ropes, the corrosion resistance of stainless-steel wire ropes is a lot more, even though it is no different in strength. This makes it the most preferred choice in water and marine-based industries.
Galvanized wire ropes are also steel wires that go through a galvanizing process to increase corrosion resistance. The galvanizing process involves immersing the wire rope in a zinc bath to completely coat the product.
The reason zinc is used in the process is that cathode protection increases the wire’s life expectancy. However, the coating will become weak over time. This will leave the wire rope open to rust and corrosion.
The last type is called coated wire rope. Stainless steel and galvanized wire rope can be easily coated with vinyl or poly-vinyl-chloride. These coated wires come in a variety of colors like white, black, or any other color if required. PVC coated wires are used as they are cost-effective and weather-resistance.
However, nylon-coated wires are not as flexible as PVC but are ideal for businesses in extremely cold regions. Regardless of the type, wire ropes can be modified to suit the needs of different construction projects.
Components Of A Wire Rope
Wire
The wire is the smallest component in a wire rope and forms the individual strands in the rope. Wires can be made using different types of metals such as stainless steel, iron, bronze, and model. Additionally, wires can be manufactured in different grades related to wear resistance, strength, corrosion resistance, and curve.
Strands
Wire ropes feature an axial member around which two or more wire strings are wrapped around in a geometric pattern or combination with steel wires and other materials. Then, these individual patterns are placed around the core in a helical pattern. The strands represent a major part that helps the wire bear heavy loads. Furthermore, wires made from larger diameter wires tend to be relatively more resistant to corrosion, while smaller diameter wire ropes tend to be more flexible.
Final Word
That’s it! So, next time you are out there looking for the perfect type of wire rope, you can choose from a wide variety based on strength, steel material, flexibility, and corrosion resistance ability. You can also take advice from rigging services MD on which rigging tools to use.